Collaborating with robots
How can collaborative robots, or cobots, help manufacturers improve productivity in a competitive marketplace? Mark Gray, UK Commercial Manager at Universal Robots, debunks a few myths.
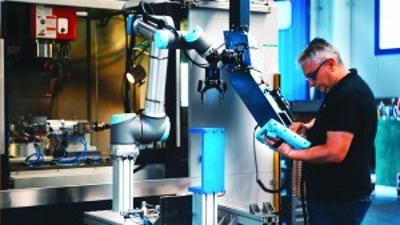
Before COVID-19, it was no secret that the UK is lagging behind mainland Europe on productivity. The manufacturing and services industries have been hit the hardest, with output per hour falling to a record 0.5% last year. This sustained period of declining labour productivity is compounded by factors including a lack of certainty surrounding Brexit, a declining workforce and the UK’s delayed adoption of workplace robots and automation compared to the rest of Europe.
Demonstrating the scale of the issue, the UK only has 10 robots for every million hours worked, compared with 133 in Germany. The connected automated technologies that are integral to Industry 4.0 are seeing increasingly rapid and widespread deployment the world over. This, in turn, is revolutionising development and manufacturing setups of products in almost every industry, from healthcare to food packaging.
As the concept of Industry 4.0 gains more and more traction, it is clear that UK businesses must invest in the skills and technologies necessary to remain competitive. However, this does not mean a shift to the lights-out factory, where all human workers are replaced with robots. To fully reap the benefits of Industry 4.0, it is necessary to reframe the concept as a balance between human skills and robot capabilities.
Currently, robots are only capable of doing what they are told, so a spark of human creativity is needed to help manufacturing setups reach their fullest potential. Overall, customers still dictate the market, and the demand for increased personalisation of products means that, with training and acquisition of new skills, humans still have a vital role to play in the changing manufacturing landscape. This is where collaborative robots – cobots – serve not as human replacements, but as an additional tool for a human worker.
Finding a balance
While the conversation surrounding robots remains largely focused on the impact on human workers, it is important to remember that the use of robots in manufacturing is nothing new. Industrial robots were first introduced in the 1960s, as part of Industry 3.0. They were most prevalent in the automotive industry, where they were mostly used to weld car bodies. As technologies became more capable, they were then incorporated in other areas, such as logistics and the medical and food industries. Since then, robots have spread to almost every sector.
Researchers demonstrate that robot-human teams are about 85% more productive than either working in isolation. In fact, according to the UK Government’s Automation and Future of Work report, even if robots do take over assembly line work, this will create newer, highly-skilled jobs in programming, quality control and back-office operations.
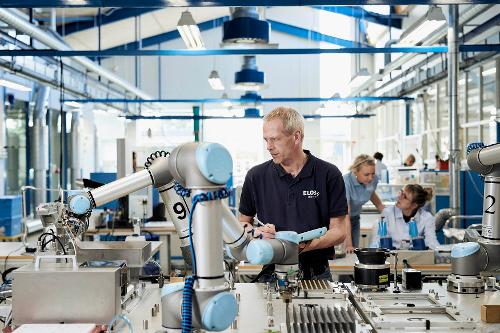
This theory is exemplified by Trelleborg Sealing Solutions. When the organisation decided to incorporate more cobots into its production setup, employees feared for their roles. However, cobot adoption resulted in employees learning new skills, and production increased to such a high level that the organisation was able to hire 50 new staff members.
Jesper Riis, Denmark-based Trelleborg Sealing Solutions Production Manager, explains, ‘We are producing at a much more competitive price than before. With flexible, lightweight robots we have a useful tool to optimise across our production network.’
The three ‘Ds’
The driving factor behind cobot adoption is a desire to reduce, or eliminate, the ‘three Ds’ – dull, dangerous and dirty jobs. Cobots can remove the need for workers to carry out repetitive, tedious or even dangerous tasks. Today’s connected, or Industry 4.0, cobots can generate data on parts flow and process quality. This data can fuel articial intelligence (AI) algorithms or be used for data analysis to optimise factories and manufacturing processes.
For example, Unilever found that it was struggling to tackle staff churn when it came to monotonous and manual packaging and palletising tasks. These tasks were also strenuous due to the product sizes involved.
‘Each year a decreasing number of people apply for positions related to palletising, but in our plants, this is a key process which has to be performed efficiently,’ explains Dariusz Ratajczak, Automation Senior Specialist at Unilever, UK. ‘For packaging, we needed a robot with enough reach of the arm. The task that the robot needed to fulfil consisted [of] picking various boxes with tea and placing them on a pallet.’ Robots also permit more flexibility than special machines and hard automation, allowing for greater product variation on a single line. Moreover, when robots are integrated with logistics systems in Industry 4.0 setups, factories can create product variations based on the customer’s choice of pre-configured options, often referred to as mass personalisation.
Product personalisation
While robot adoption allows manufacturers to increase production, awareness of market demands and responsiveness to change are also essential for businesses to stay competitive. Customers expect a higher level of personalisation in their products, meaning that agility and freedom to adapt the production line is crucial. Robots, and other connected Industry 4.0 technologies, are making it possible for manufacturers to adopt mass customisation. This is facilitated by connections between Industry 4.0 technologies – including internet connections between dealership ordering systems, supply chain systems and robots on the factory floor.
This is where human skills, such as problem-solving, creativity, and the ability to understand customer needs on a deep level become integral to production setups. These are qualities that robots may never be able to replicate, so it stands to reason that organisations must create setups that enhance collaboration between man and machine and combine the best of both worlds. This will ensure more robust ways of working that improve the overall longevity and competitiveness of organisations.
With all these benefits in mind, nonetheless, the cost factor is a huge hurdle for smaller businesses in adopting cobots for product personalisation. However, because of the worldwide price consistency of robots, they can help companies re-shore manufacturing jobs that have been outsourced to low-cost labour countries, as well as levelling the playing field in general.
In the case of B-Loony, UK SME manufacturer of bespoke promotional products, ‘all our products are customised and we don’t have the luxury of unlimited space in our production facility, so incorporating industrial robots, caging or safety guarding is difficult’, says Operations Director James Clephan. ‘However, I could instantly picture how the cobots would slot seamlessly into our operations.’
B-Loony was able to enhance the production abilities of existing human workers and allow for mass personalisation of products. As Clephan explains, ‘Despite rising inflation and labour costs, investing in robotics and automation has made us more efficient and able to compete.’ This productivity and agility increase has resulted in B-Loony achieving a payback period of just nine months, which is expected to be brought down further in its future projects.
With political unease and the economic downturn contributing to decreasing productivity in UK manufacturing, this has increased the pressure for organisations to adopt innovative and cost-effective solutions. Rather than being viewed as a threat to UK jobs, cobots should be reconsidered as the ‘helping hand’ that allows manufacturers to keep pace with demand and diversify their outputs.
For the UK to stay competitive in a global marketplace, cobots should be viewed as a future investment with the flexibility to adapt to changing circumstances and evolve with companies. They also offer a valuable opportunity for companies to ensure employees adapt to a fast-changing work environment and learn new skills. With untold benefits to the manufacturing industry, the time is now for organisations to start harnessing the benefits of cobots.