Clear vision – anti-fogging coating on plastic lenses
Scientists at Nanyang Technical University (NTU) Singapore have developed an anti-fogging coating for plastic surfaces that they claim also self-cleans.
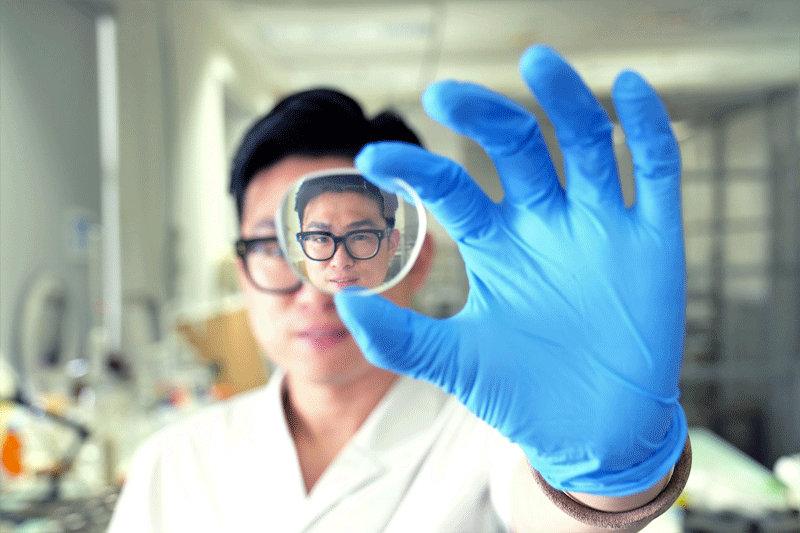
The research team noticed that wearers of face masks with eyeglasses needed anti-fogging sprays and wipes, which need regular reapplication and endure surface contamination.
Anti-fogging coatings are used for solar panels, windshields, displays and lenses in humid environments, but such coatings for plastic have not had wide adoption – mostly due to a long manufacturing time and weak adhesion.
The new thin-film coating is a silicon-dioxide-titanium-dioxide double layer. After the plastic surface is cleaned with oxygen plasma, pulse laser deposition applies the coating so excess material is vaporised, leaving a 50-60nm thickness which works best for anti-fogging.
The coating is said to have excellent adherence and good durability – even from cheese cloth pad abrasion, a standard optical coating test, and an adhesion test using cellophane tape.
Co-principal investigator Professor Chen Zhong says, ‘Silicon dioxide possesses the surface wetting properties ideal for anti-fogging. As an oxide, it has better mechanical properties against cloth wiping actions or mild particle scratch/impingement than organic coatings. In terms of production cost, silicon dioxide is among the most inexpensive oxides that industry can produce.’
Anti-fogging performance is measured by how fast condensed water droplets spread into a uniform film. Digital fast-frame imaging shows that a water droplet on the new coating spreads within 93ms, less than the time it takes to blink.
The self-cleaning element is made from the titanium dioxide which is photocatalytic – it removes organic residues when it reacts with ultra-violet (UV) light.
Contaminants such as bacteria and dirt are broken down after a full day of UV light exposure, so far tested in the lab with LED lights. Chen recognises, however, that this could be faster. ‘Indeed, it does require quite some time to degrade the organic contaminants, and the degradation speed clearly depends on the level (concentration) of the contamination.’ The amount of UV light the coating is exposed to is also a factor, which is why Chen admits that field tests may be necessary.
The new coating is also anti-reflective and has 89% visible light transmittance, which researchers claim is about 5% better than the same lens without the coating. This is particularly useful for eyeglasses, as more light can reach the eye.
‘Oxide is the most stable material in the world. Therefore, there is no worry on its degradation under UV exposure like a plastic. Therefore, the oxide coating itself in theory can last ‘forever’ if UV degradation is the only concern,’ Chen says. ‘Assuming proper usage and care, we believe our coating can last for months or even years.’
He explains that short-term damage would likely be from scratching, such as grit, which they want to improve.
Chen adds, ‘It should work on most plastics. In our laboratory, we used polycarbonate and ZEONEX (a commercial plastic lens material). It can also be applied to glass or other ceramics.’
As well as eyeglasses, potential applications are solar panels, windshields, displays, microscopes, face shields, motorbike visors, car mirrors, road convex mirrors and surveillance cameras. It could also be used in goggles and snorkel masks.
A patent is pending and the team is seeking industrial partners for collaboration.