Biomass-based plastic to take on PET?
A biomass-derived PET-like material could finally offer a competitive alternative to current plastics.
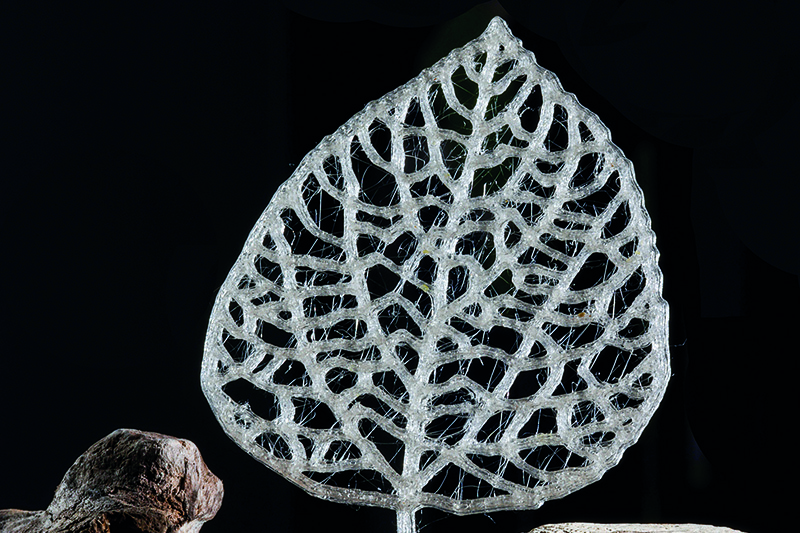
The plant-based plastic is reportedly tough, heat-resistant and an effective barrier to gases like oxygen for food packaging - claim scientists at the École Polytechnique Fédérale de Lausanne, in Switzerland.
The developers say that, unlike other lignocellulosic biomass plastics, this rivals conventional plastics for cost, heat stability, mechanical strength, processability, and compatibility. It can be chemically recycled and degrades to harmless sugars.
'We essentially just ‘cook’ wood or other non-edible plant material, such as agricultural waste, in inexpensive chemicals to produce the plastic precursor in one step,' says Professor Jeremy Luterbacher. 'By keeping the sugar structure intact within the molecular structure of the plastic, the chemistry is much simpler than current alternatives.'
The process uses a 2016 discovery by Luterbacher and colleagues, who found that adding aldehyde stabilises certain fractions of plant material to avoid destruction during extraction. Repurposing this has allowed the researchers to rebuild a
bio-based chemical as a plastic precursor.
First author Lorenz Manker explains that any lignocellulosic feedstock is theoretically usable – wood, corn cobs, rice husks, grasses, nut shells, fruit pits, wheat straw – which all have differing amounts of cellulose, hemicellulose and lignin.
'Our polymer is made using sugars from the hemicellulose fraction, therefore, the most sensible biomass to use are ones that have high hemicellulose content, such as corn cobs.' Manker says that as homogenous feedstock is more efficient at larger scale, one type of biomass per producton plant is preferable.
In the laboratory, the researchers cook the material at 70-120°C for one to three hours with the biomass, glyoxylic acid, a mineral acid, and sometimes a solvent.
Manker says that as the biomass degrades in acid through dehydration reactions, glyoxylic acid – an aldehyde – is used to block the reactive sites, stabilising the biomass and preventing degradation. It also adds a ‘sticky’ group onto either side of the sugar molecules. This is mixed with another molecule with compatible sticky groups which, when both are heated to around 200°C, form long polymer chains to make the plastic.
'By using a different aldehyde – glyoxylic acid instead of formaldehyde – we could simply clip ‘sticky’ groups onto both sides of the sugar molecules, which then allows them to act as plastic building blocks,' shares Manker. 'By using this simple technique, we are able to convert up to 25% of the weight of agricultural waste, or 95% of purified sugar, into plastic.'
The resulting PAX plastic is reported to withstand higher temperatures before losing its form than PET. Manker says, 'For example, it can withstand boiling water (100°C) without losing its strength, whereas PET would wilt around 80-90°C. Our plastic is also mechanically stronger, but it is less flexible. Also, our plastic is just as good as PET at preventing oxygen from getting through it (to keep food from spoiling), but it is slightly worse in terms of sealing in/out water.'
While the researchers have only made a few kilogrammes as packaging films, textiles fibres and 3D-printed filaments, they believe there is commercial potential, as PET and other plastics are made using melt polymerisation.
Meanwhile, Manker says the plastic is a good use of waste material with no other purpose. Regarding recyclability, he points out that although PET is chemically recyclable, its properties diminish each time. He says, 'PAX can be easily recycled chemically, meaning we can depolymerise the plastic back to building blocks, purify them, and repolymerise them back into a virgin material without loss of properties. This can even be done from a mixed plastic stream...'