Better battery recycling
Researchers from the Chalmers University of Technology, Sweden, have identified ways to optimise electric vehicle battery recycling after comparing industrial processes.
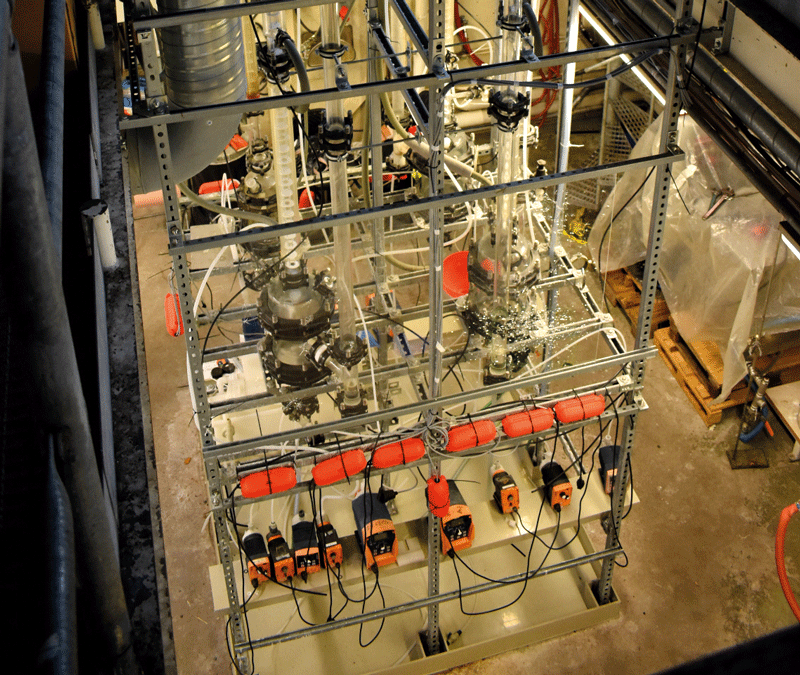
The researchers have examined two thermal pre-treatment approaches – incineration and pyrolysis – alongside hydrometallurgy, which uses aqueous chemistry to recover metals, such as through precipitation, solvent extraction and ion exchange. The team has discovered widely differing temperatures and process times across the sector.
A key finding, not previously tested, is that hydrometallurgy can actually occur at room temperature. In some cases temperatures can be reduced from 60°C, or even 80°C, with process times coming down from several hours to 30 minutes.
The team says they always do a kinetic study when investigating leaching, to find out how much metal dissolves in a defined period. They think companies use high temperatures to try and speed up their process because it is not optimised.
While for thermal pre-treatment, pyrolysis, which occurs without oxygen, is deemed to be more successful than incineration at reducing complex oxides to less complex oxides or their metallic forms, while also avoiding oxidation of the copper and aluminium foil from the current collectors.
‘To meet the huge need for battery recycling that is coming, the processes currently in use must be made as effective and efficient as possible, so this study offers invaluable knowledge for the manufacturers and operators of this technology. The methods we present can also be used to optimise the recycling of all kinds of lithium-ion batteries,’ explains Associate Professor Martina Petranikova, who has also worked with battery manufacturer Northvolt to develop and implement their recycling processes.
The paper published in the journal Waste Management, by Elsevier, concludes, ‘Although increasing the incineration temperature does not promote any clear benefit to the leaching yield or kinetics, the temperature does have a positive impact on pyrolysed samples. The leaching yield is improved when the pyrolysis temperature increases.’
It reports that all lithium, manganese, cobalt and nickel can be leached through pyrolysis at 700°C, with ‘a gradual improvement in the leaching yield’ when the pyrolysis temperature is increased from 400-600°C.
Moreover, ‘for pyrolysis at 700°C, increasing the time of thermal treatment decreases the leaching yield from 100% in 30 and 60 minutes, to 70% in 90min for cobalt and nickel. Kinetics are also slower when the time is increased’.
They conclude, on considering all the variables. that pyrolysis at 700°C for 30 minutes are the best parameters.
The paper reads, ‘Under these conditions, full recovery via leaching with sulphuric acid at ambient temperature is reached after two minutes for lithium, five minutes for manganese and 10 minutes for both cobalt and nickel.
‘Performing pyrolysis before the leaching in a lithium-ion battery recycling process is a promising pre-treatment approach, which cannot only ease the industrialisation of recycling, but also the pyrolysis products can be reclaimed.’
Petranikova continues, ‘We are focusing on lithium-nickel-manganese-cobalt-oxide (NMC) type [batteries] and lithium-iron-phosphate (LFP) type [batteries] since those we can expect to come back from the market in upcoming years. Even though new types are being developed, it will take a long time until they are manufactured, used and obsolete. But when the time comes, we will develop/optimise the technologies for their recycling in advance.’
When asked if battery producers should be given responsibility for recycling, Petranikova points out that Extended Producer Responsibility already exists, and that it is more important that the recycling is done in the most effective and environmentally friendly way. She adds that the best model is when the battery producer is also a battery recycler since they know when to stop in the purification steps, and that saves energy, chemicals and time.
Solid-state batteries contain significantly more different metals, making recycling even trickier. Petranikova thinks regulations will help to control the number of metals used. ‘Well, I always say that my dream battery is without the aluminium and fluorine, but that is currently not possible. It is not easy to say the number, but it would be great not to use too low amounts or metals which are chemically too similar and then very difficult to separate from each other,’ she says.
She also points out that many chemicals used in the process can be reused, whereas in pyrometallurgy they are all consumed. Thermal pre-treatment can decrease chemical consumption.
The team is now focused on optimising lithium recovery, and consumption of chemical reagents and energy. Petranikova says, ‘We want to get as low as possible without affecting the efficiency. We are also looking into solid-state batteries recycling.’