Aligned thinking – connected materials handling
Sven Kruizenga at Toyota Material Handling Europe, on connectivity, smart manufacturing and the impact of Industry 4.0.
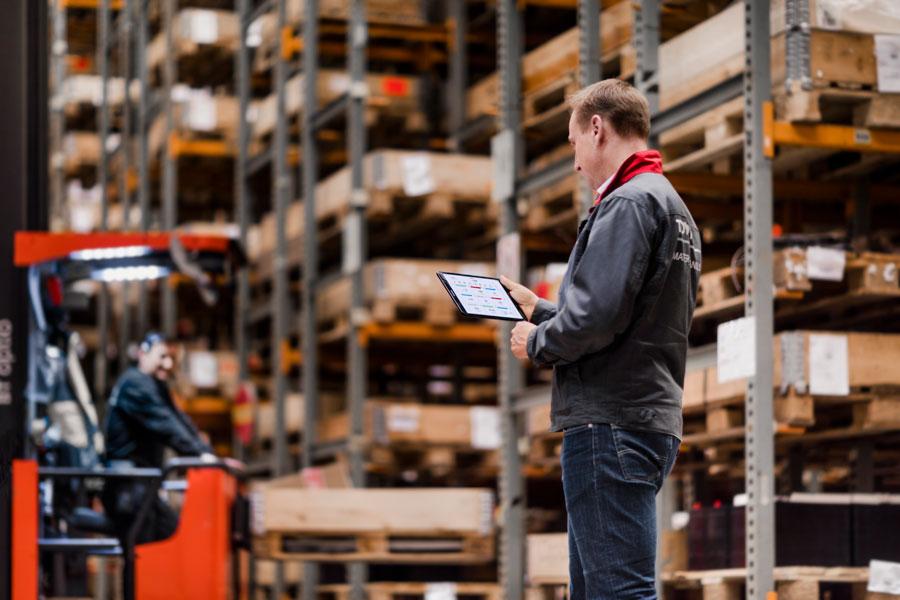
What have been the major shifts in material handling over the past decade?
Material handling has been a traditional industry for many years as moving goods from A to B is nothing new. Where we have seen the biggest shifts in the last decade has been in moving to more automated solutions that offer 24/7 operations and optimise space by not needing driving aisles, as automated and autonomous trucks can navigate more easily through racks and warehouses.
We have also seen more focus around the data of material handling operations and how this can improve operations by minimising costs, optimising safety, and becoming more sustainable. Connectivity and the data that we now gather from over 160,000 connected trucks operating around the globe allow us to do exactly that, as we can learn what is going well and improve operations based on the facts coming from the numbers.
Gathering data from our forklift trucks is again nothing new, but being able to tap into the data from a large source and applying analytics and data learning to this is where the biggest differences are.
What does the future of material handling look like?
Integrated supply chains and more complex logistics will be challenges for the material handling industry – both are issues that need to be overcome if the sector is to continue to innovate and find ways to move (smaller) goods in smart and affordable ways. With shortages of certain core materials, this approach will become more important.
To support this transition (and to best advise clients), we need to understand and learn from the data we gather from our trucks. This will make the biggest difference over the few years as we gather more intelligence to improve logistics. This is only possible by linking the new technological innovations with analytics and machine learning.
Do clients see risks when adopting new technologies?
Most customers are open to adopting new technology as they understand the additional value it can bring to improving their operations. We saw similar shifts when introducing lithium-ion batteries to material handling. Once people trusted the technology – for example, in the use of their own cell phones – they were more open to adopting them in their logistics operations.
We see a similar adoption when it comes to using data to generate insights. Again, much of what we use in our everyday lives is connected through our cell phones – including our cars and even controlling the heating of our homes. The reluctance comes from being able to secure and handle the data in a sensitive and safe way, as we are dealing with operational and personal data that are, in many cases, core to customer operations – of course you would not want this information to fall into the wrong hands.
What are the sustainable advantages of smart, ‘connected’ forklift trucks?
Understanding exactly how your trucks are being used helps to determine the right investments, for example, if you want to replace a truck or keep it running. Metrics analysed include intensity of performance, or if it has endured much damage and energy consumption. These are all topics that should be considered when making operating decisions.
Smart or connected trucks gather exactly this information, and by comparing this to other models, allows for a sustainable approach to the fleet’s operation. Simply put, no measurement can mean no improvement.