4D composite printing shapes bendable wings for drones
4D composite printing could lead to morphing wings on drones. This would replace a common hinged wing flap.
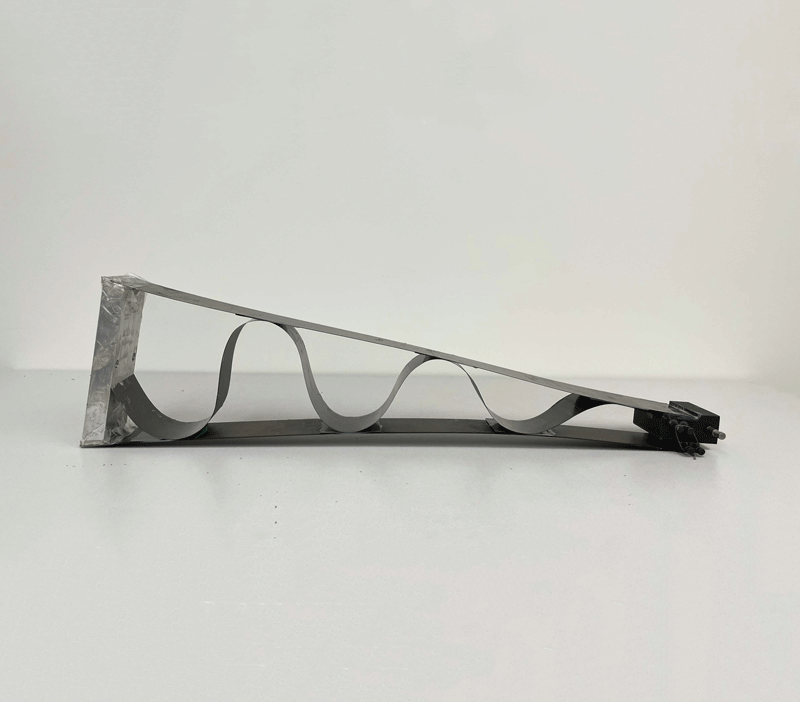
Pressures on the aviation sector, such as rising fuel costs and environmental awareness, are motivating researchers to investigate cost-effective efficiency gains, including for unmanned aerial vehicles (UAVs), or drones.
Professor Suong Hoa, at Concordia University in Canada, developed the 4D composite printing technique which has led to a feasibility study on manufacturing adaptive compliant trailing edge morphing wings.
Unlike 3D printing, 4D printing changes materials from location to location – it includes a material that reacts to stimulus such as water, cold or heat. After being printed flat, the composite changes into a 3D-shape when exposed to stimuli. The fourth dimension refers to the altered configuration of the once-flat material.
While 3D printing requires a soft and dough-like supply material, 4D printers use long, fine filaments held in place by a resin. Each filament is only 10µm thick. According to Hoa, the 4D technology works with different fibre and matrix materials, so long as there is some degree of anisotropy.
The 4D composite printer unrolls the filament-resin mixture in ultra-thin layers that are perpendicular to each other. The layers are then compacted, cured at 180°C, and cooled to 0°C, to create a stiff object that is not brittle.
Hoa explains, “The material we use is carbon/epoxy composites…The fibre content is about 60% by weight. The printer is an automated fibre placement machine. It prints out strips of the prepregs. We print one strip at a time. Many strips side-by-side make a layer. Each layer has a certain fibre orientation. The fibre orientation varies from layer-to-layer. For example, layer one can have fibre orientation at 0°, while layer two may have fibre orientation at 90°. The layers are deposited on a flat surface. After curing and cooling to room temperature, the anisotropy in the different layers creates the curvature. The shaping is controlled by the different fibre orientations.”
The scientists say that the material of uniform curvature can be fixed between a wing flap’s upper and lower surfaces, making it flexible enough to deform by 20° during flight. This was verified in a static test, when the wing was subjected to cantilever loading. When the load is relieved, the shape returns to its initial configuration, enabling the process to be repeated multiple times.
“We have developed composite leaf springs. These can be made without need for a curved mould,” says Hoa. “You package things in flat shape. On arrival at the destination, you activate the heating or cooling to change the shape to curved. This can have applications for sending shipments to remote locations such as outer space or the North Pole.”
The next step is to test the UAVs for lift and drag as a function of the design, as well as developing other applications. The team are currently trying out different materials.