3D printing titanium alloys
Additive manufacturing (AM), also known as 3D printing, can produce super-strong, highly ductile and ultra-light titanium alloys, according to a materials research team at City University of Hong Kong, China.
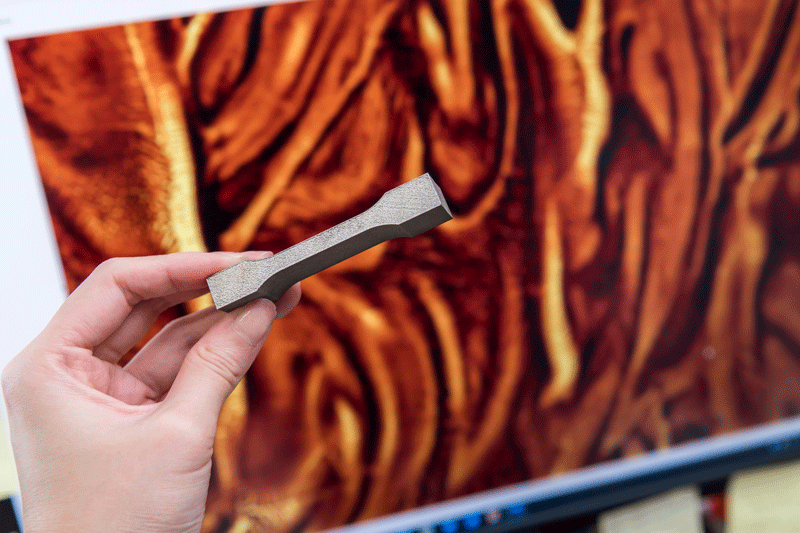
Researchers say the process produces titanium that is 40% lighter in weight, with lava-like microstructures exhibiting a high tensile strength of about 1.3GPa, a uniform elongation of about 9%, and work-hardening capacity of over 300MPa.
The process has been designed ‘using two commercial alloy powders: Ti-6Al-4V (Ti64) and 316L stainless steel,’ shares the paper, In situ design of advanced titanium alloy with concentration modulations by additive manufacturing, published in Science.
It reads, ‘We demonstrate an in situ design approach to make alloys spatially modulated in concentration by using laser-powder bed fusion. We show that the partial homogenisation of two dissimilar alloy melts allows us to produce micrometre-scale concentration modulations of the elements that are contained in 316L and in the Ti-6Al-4V matrix.
‘The corresponding phase stability modulation creates a fine scale–modulated dual-phase microstructure that exhibits a progressive transformation-induced plasticity effect. This approach creates a pathway for concentration-modulated heterogeneous alloy design for structural and functional applications.’
Dr Zhang Tianlong, a Postdoctoral Researcher at the University, explains that while AM has become more and more important in modern society, the success and wide application of metal-based AM has been severely hindered by the lack of printable alloys and the relatively poor mechanical properties of most AM-produced components.
He says, ‘People always consider 3D printing only as a shaping technology to form a complex component in one-step, without taking the full use of AM in alloy design. So, they only design materials for 3D printing, instead of designing materials by 3D printing.
‘Metallurgists mostly consider that the inhomogeneities in alloy components are undesirable which leads to bad properties. In the AM community, one of the key issues is how to eliminate such inhomogeneity during fast cooling. However, seldom have the researchers tried to turn such waste into wealth.
‘By controlling the fluid dynamics within the melt pool and creating alloys from partial homogenisation, we have achieved a gradient microstructure with a micrometre-scale concentration heterogeneity in situ throughout the bulk materials, which correspondingly leads to excellent structures and properties.’
Tianlong explains that it is the iron concentration included in 316L powders that increases the supercooling capacity of the alloy melt during solidification, leading to finer solidification grain size. The iron concentration also plays an important role in determining the phase stability during fast cooling, which influences the final microstructure.
He says, this ‘alloy design strategy opens a new area of AM in the design of unprecedented alloys that are unachievable by any conventional methods.
‘On the other hand, the designed titanium alloys with excellent properties are promising for structural applications in various scenarios, such as aerospace, automotive, chemical and medical industries’.
The research team aims to now carry out more detailed tests of the properties under different circumstances, and explore their application in a range of alloy systems as well as application scenarios.
Also see Materials World, November 2021, for an article on 3D-printed copper-silver alloys at bit.ly/3n2MNIC.