3D-printed phase change composites regulate building temperature
Phase-change material composites that can regulate ambient temperatures inside buildings are being developed at Texas A&M University, USA, using a ‘simpler and cost-effective manufacturing process’.
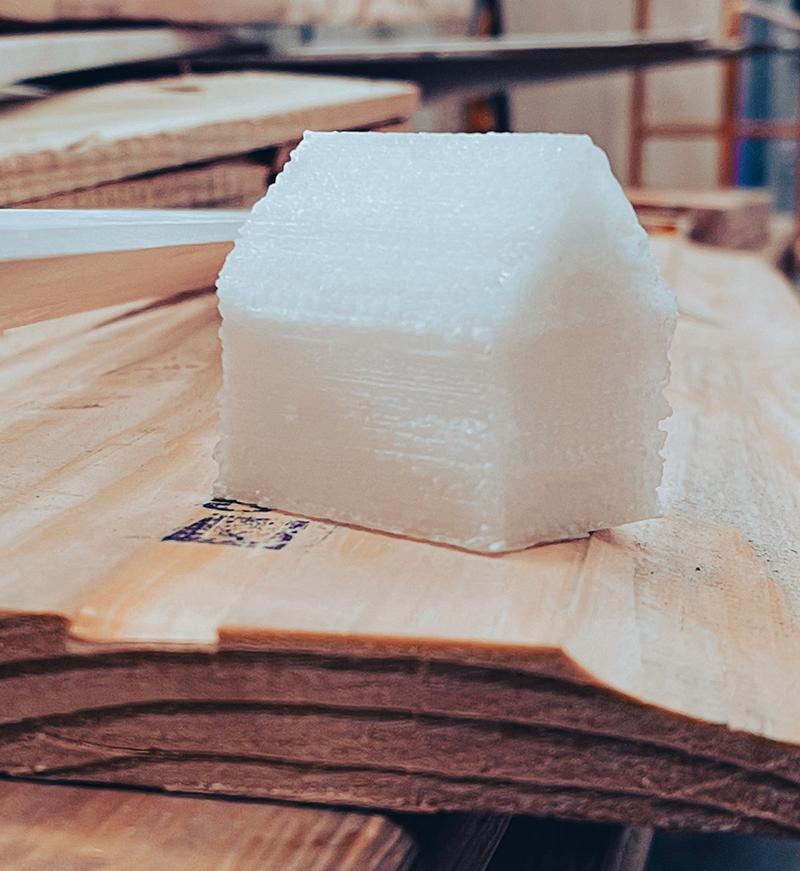
or 3D printed for decorative features © Texas A&M University
The researchers suggest they could be added to building materials like paint, or 3D-printed as decorative features.
The traditional approach to manufacturing PCM building materials requires forming a separate shell around each PCM particle, then adding these newly encased PCMs to building materials. However, finding building materials compatible with both the PCM and its shell has been a challenge. In addition, this conventional method also decreases the number of PCM particles that can be incorporated into building materials.
To overcome these challenges, past studies have shown that when using phase-changing paraffin wax mixed with liquid resin, the resin acts as both the shell and building material. This method locks the PCM particles inside their individual pockets, allowing them to safely undergo a phase change and manage thermal energy without leakage.
However, the resin/PCM mixture, while soft, paste-like and malleable for 3D printing, is not suitable for building structures. The team at the University have discovered that by using a light-sensitive resin, they can cure it with an ultra-violet (UV) light to solidify the 3D-printable paste so that it can be incorporated into building materials.
To develop the material, the team creates small particles of PCM by first heating it above its melting point, followed by forming an emulsion, then cooling to room temperature, explains Emily Pentzer, Associate Professor at the University. ‘This resulted in PCM particles that were [micrometres] in diameter.
‘We then took these particles and simply added them to a vial of the liquid resin. When enough of the PCM particles are added, an ink is formed, which has the consistency of toothpaste. This means that…once it’s been printed, it doesn’t lose the shape. We then use a pen with UV light to ‘cure’ the ink, which essentially takes the resin part and cross-links it around the solid PCM.
‘This structure can then be heated up and the PCM absorbs the thermal energy and melts, but stays encased in the printed structure. This allows it to be melted and solidified for many, many cycles.’
Pentzer adds, ‘A major benefit of these composites is that they are simple to make in only two steps. More than that, this approach can be used for many different types of PCMs.
She says the different PCMs have different temperatures at which they melt and solidify, meaning that they have different uses, depending on the temperature range that they want to control. ‘So, with our method, you can tell us what temperature you want to control and we can pick the PCM. We can also incorporate multiple types of PCM into the same structure, which gives a broader operating temperature window.’
Unlike heating, ventilation and air conditioning (HVAC) systems, the most commonly used methods to regulate building temperatures, the materials do not require external power to heat and cool as they are passive components.
‘These materials regulate temperature much like the PCM by itself,’ Pentzer notes. ‘When the temperature rises, the solid particles undergo a phase change to liquid – then when the temperature decreases, the opposite phase change occurs, and heat is released.
‘With the ability to 3D print these structures, we envision those decorative parts on the inside of a building, such as molding, can be prepared. So, this would be applicable to new buildings as well as capable of modifying existing buildings.’
Demonstrating proof-of-concept, the team will now look to test the materials in real situations to monitor how they impact building temperature.
‘Our next steps are increasing the energy density and making sure the PCMs perform at temperatures relevant to the type of settings we want to do thermal energy management,’ says Pentzer. ‘We’ve demonstrated that the materials can be made and that they have very promising performance on the small scale but now we need to show more.’